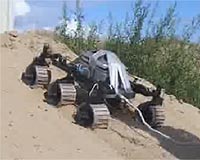
As interest in exploration of the Moon soars among the world's space agencies, ESA, through it's General Studies Programme, has challenged university students to develop a robotic vehicle that is capable of working in difficult terrain, comparable to that found at the lunar poles.
Eight university teams have been selected to proceed to the design stage of ESA's Lunar Robotics Challenge.
ESA's first Lunar Robotics Challenge got under way in late March with the issuing of an Announcement of Opportunity that invited teams of university students to create an innovative, mobile robot capable of retrieving samples from a lunar-like crater.
Eight of the submitted proposals have been selected for funding after evaluation by a team of ESA experts. The selected student teams received the go-ahead to design their robotic systems, and eventually build them to compete in the challenge event.
Challenge objectives
The proposals had to describe the design of a vehicle capable of retrieving soil samples from a crater, and an associated remote-operation workstation. The vehicles are required to weigh no more than 100 kg, consume no more than 2 kW of power, and occupy a volume of no more than 0.5 cubic metres with deployable appendages stowed.
The robot's test mission includes a number of objectives:
- move from a 'landing site' to the rim of a lunar-like crater
- descend into the crater, negotiating an incline of up to 40 degrees
- operate in sunlight on the crater rim, and in the dark interior of the crater
- reach the bottom of the 15 m deep crater
- locate and retrieve at least 0.1 kg of selected, visually distinctive, soil samples from the bottom of the crater
- return to the crater rim and then the 'landing site'
- The vehicle will be remotely operated by a workstation placed outside the crater and with no direct visibility of the crater or rim.
Selected teams
The teams selected to proceed with the design phase, supported by funding from the ESA General Studies Programme (GSP), are:
Universität Bremen, Germany,
University Bremen, Germany,
Universidad Politecnica de Madrid, Spain,
Oulun Yliopisto (University of Oulu), Finland
Università di Pisa, Italy,
Scuola Superiore Sant'Anna Pisa, Italy,
Surrey Space Centre, University of Surrey, United
Swiss Federal Institute of Technology (Eidgenossische Technische Hochschule - ETH) Zurich, Switzerland
Each team is required to maintain a web blog during the challenge.
Reviews and competition
Following the selection, a kick-off meeting for the successful entrants was held by videoconference. The student teams were then given a few months to develop their design ready for a Critical Design Review (CDR) to be held at ESA's European Space Research and Technology Centre (ESTEC), in the Netherlands, on 9 and 10 July.
If they are successful at the CDR, the teams will be given approval and further funding to build their entry.
A Test Readiness Review will be held at the premises of each university team once construction of their robot is complete. The challenge will culminate in a 10-day competition, to be held in October 2008.
----------------
Listening to: Metalica - Nothing Else Matters
via FoxyTunes